Procurement and inventory management are critical components of a successful business operation. These interconnected processes ensure that companies have the right products at the right time, while minimizing costs and maximizing efficiency.
This article explores the various facets of procurement and inventory management, providing actionable insights into optimizing these processes for better efficiency and growth.
What is Procurement and Why is it Important for Inventory Management?
Procurement is the process of sourcing and acquiring goods and services that a company or organization needs to fulfill its operations.
Effective inventory procurement ensures that the right products are purchased at the right price and delivered at the right time. This is crucial for inventory management, which revolves around maintaining the optimal stock quantity to meet customer demand while minimizing costs.
How Can Businesses Optimize the Procurement Process?
To optimize procurement, businesses should:
- Streamline sourcing strategies
- Leverage technology for better vendor management
- Implement strong negotiation practices
- Use data from inventory management to inform purchasing decisions
What Are the Key Components of an Effective Inventory Management System?
An effective inventory management system incorporates:
- Real-time inventory tracking
- Demand forecasting
- Robust reporting tools
- Automated reordering systems
These components help businesses maintain accurate stock levels, reduce waste, and improve supply chain efficiency.
How Can Businesses Forecast Demand to Improve Procurement and Inventory Control?
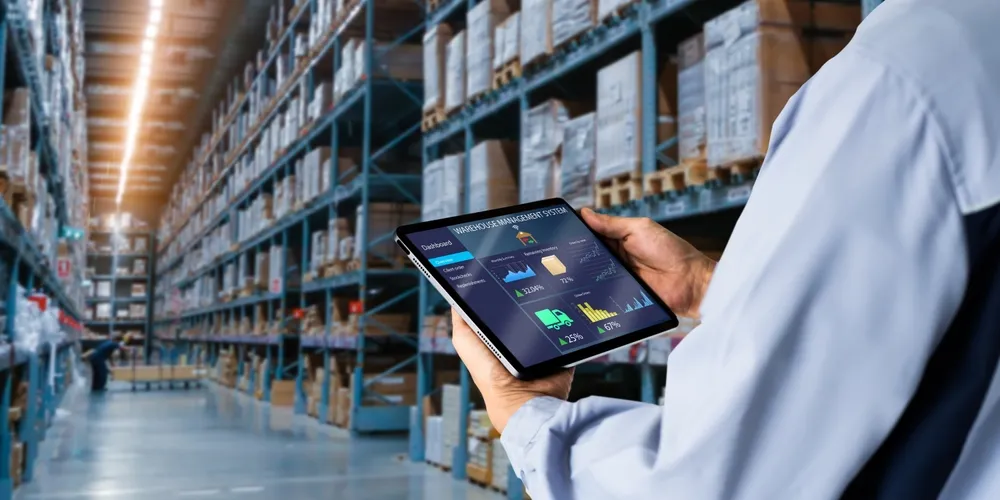
Demand forecasting combines historical data, market trends, and statistical models to predict future customer demand.
By accurately forecasting demand, businesses can:
- Optimize procurement schedules
- Adjust inventory levels
- Avoid overstocking or stockouts
What Are the Best Inventory Control Methods for Businesses?
Before diving into the specific methods, it’s important to understand that each business might require a different approach based on its unique needs and objectives.
Below are some of the most effective inventory control methods:
Just-in-Time (JIT) Inventory Management
JIT is a strategy where materials are ordered and received only as they are needed in the production process. This minimizes inventory holding costs but requires precise demand forecasting.
Economic Order Quantity (EOQ)
EOQ is a formula that determines the optimal order quantity that minimizes total inventory costs, including ordering and holding costs. It helps businesses save on costs by balancing order size and frequency.
ABC Analysis
ABC Analysis segments inventory into three categories (A, B, and C) based on their importance and value. ‘A’ items are high-value, low-quantity; ‘B’ items are moderate-value, moderate-quantity; and ‘C’ items are low-value, high-quantity. This helps prioritize management efforts on critical items.
First-In, First-Out (FIFO)
FIFO is an inventory management method where the oldest stock (first-in) is used or sold first (first-out). This method is particularly useful for perishable goods and helps reduce inventory obsolescence.
Last-In, First-Out (LIFO)
LIFO is the opposite of FIFO, where the most recently received stock (last-in) is used or sold first (first-out). This method can benefit businesses facing rising costs, as it matches current costs against current revenues.
Reorder Point (ROP) System
The ROP system alerts businesses to reorder an item when its stock level falls to a predetermined point. This method helps ensure that stock is replenished before it runs out, maintaining steady supply levels.
Vendor-Managed Inventory (VMI)
In VMI, the supplier is responsible for managing and replenishing inventory based on the retailer’s needs. This partnership reduces the retailer’s inventory holding costs and improves supply chain efficiency.
Consignment Inventory
In consignment inventory, the supplier retains ownership of the stock until it is sold. This reduces the financial risk for the retailer and allows for flexible inventory management.
Two-Bin System
The two-bin system keeps two bins of inventory: one for immediate use and the other as a reserve. When the first bin is empty, it signals the need to reorder. This simple method ensures continuous supply without overstocking.
Drop Shipping
Drop shipping allows businesses to sell products without holding inventory. When a customer orders, the product is shipped directly from the supplier to the customer, reducing holding costs and the risk of surplus inventory.
How Can Businesses Maintain Optimal Inventory Levels Without Over-Stocking or Under-Stocking?
To maintain optimal inventory levels, businesses should:
- Use inventory management systems with real-time data
- Implement demand forecasting tools
- Set up reordering alerts
- Regularly review and adjust inventory policies
- Consider safety stock for critical items
What Are the Benefits of Automating Procurement and Inventory Management?
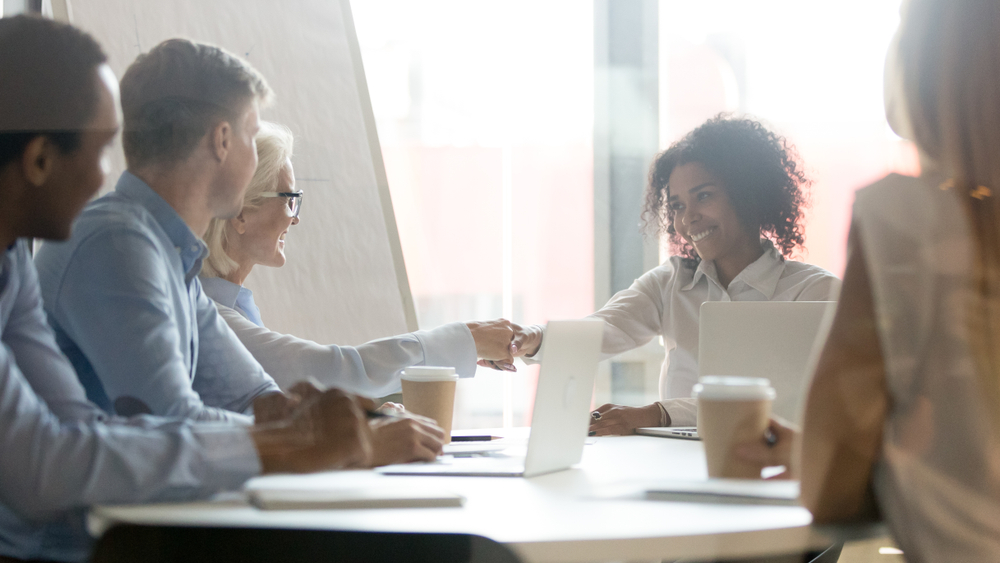
Automating procurement and inventory management streamlines processes, reduces human error, improves accuracy, and enhances efficiency. It allows businesses to focus on strategic initiatives rather than mundane administrative tasks.
How Can Businesses Build Strong Relationships with Suppliers to Improve Procurement Efficiency?
To build strong supplier relationships, businesses should:
- Engage in transparent communication
- Practice fair negotiations
- Adopt partnership-driven approaches
- Share forecasts and plans with key suppliers
- Implement supplier performance metrics
What Are the Risks of Poor Procurement and Inventory Management?
Poor procurement and inventory management software can lead to stockouts, overstocking, increased operational costs, and reduced customer satisfaction. It can also disrupt the supply chain, leading to delays and financial losses.
Strategizing for Success with LSI’s Expertise
Effective procurement and inventory management are critical for business success. By adopting advanced methodologies, leveraging technology, and maintaining strong supplier relationships, businesses can achieve superior efficiency and growth.
Regular review and optimization of these processes can lead to significant cost savings and improved customer satisfaction.
To learn more about how to optimize your procurement and inventory management processes, consider consulting with experts such as LSI or exploring advanced software solutions tailored to your business needs.